What Is the Hydrometallurgy Process for Lithium Ion Battery Recycling?
The hydrometallurgy process for lithium-ion battery recycling is a cutting-edge, eco-friendly method to recover valuable metals like lithium, cobalt, nickel, and manganese from spent batteries. Unlike pyrometallurgy, which relies on high-energy smelting, hydrometallurgy uses aqueous chemistry to dissolve and extract metals, achieving higher purity and lower environmental impact. This process is ideal for businesses handling large volumes of end-of-life batteries and seeking cost-effective, sustainable solutions.
Key Steps in the Hydrometallurgy Process
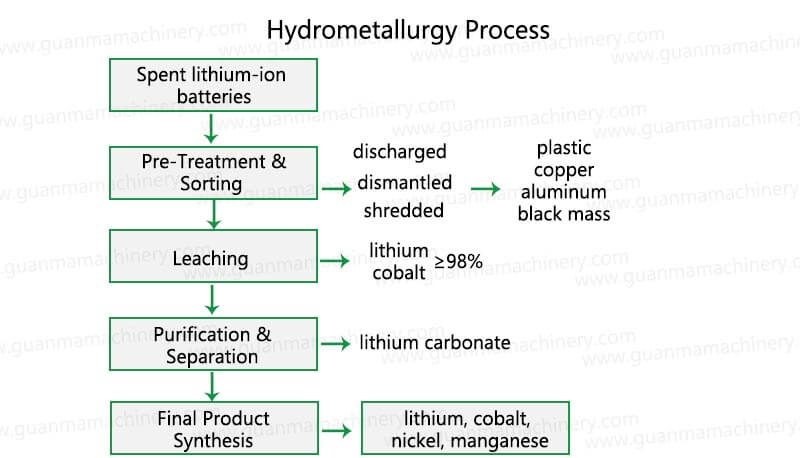
1. Pre-Treatment & Sorting
Spent lithium-ion batteries are discharged, dismantled, and shredded into black mass (a mixture of cathode/anode materials). Sorting ensures separation of plastic, copper, and aluminum for independent recycling.
2. Leaching
The black mass undergoes acidic or alkaline leaching (e.g., using H₂SO₄ or HCl) to dissolve metals into a solution. Advanced leaching agents maximize metal recovery rates (up to 98% for lithium and cobalt).
3. Purification & Separation
Solvent extraction, precipitation, or ion-exchange techniques isolate target metals. For example, cobalt is separated using D2EHPA, while lithium is precipitated as lithium carbonate.
4. Final Product Synthesis
Recovered metals are refined into battery-grade materials like Li₂CO₃, NiSO₄, or Co₃O₄, ready for reuse in new batteries.
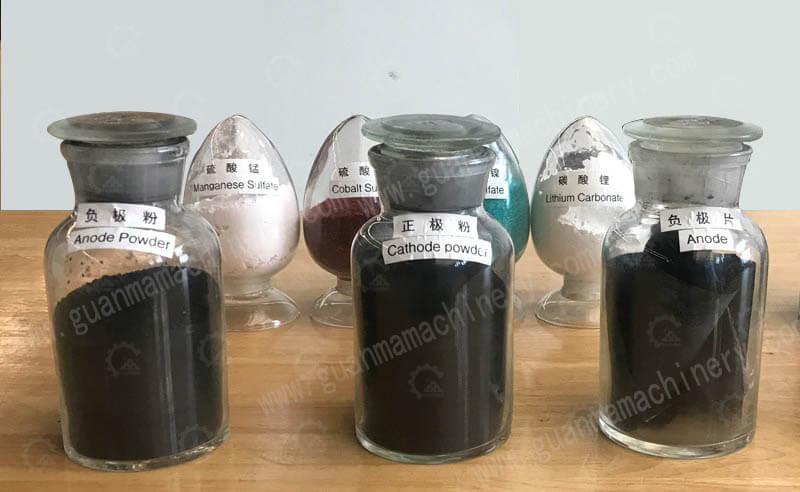
Raw Materials & Daily Processing Capacity
This process handles spent lithium-ion batteries from EVs, consumer electronics, and industrial storage systems. Common battery types include:
NMC (Nickel-Manganese-Cobalt)
LCO (Lithium Cobalt Oxide)
LFP (Lithium Iron Phosphate)
Daily processing capacity varies based on plant size:
Small-scale facilities: 1–5 tons of batteries per day.
Industrial plants: 50–100+ tons daily.
Hydrometallurgy scales flexibly, making it suitable for startups and large recyclers alike.
Final Products: Turning Waste into Value
The hydrometallurgy process produces:
Lithium Carbonate (Li₂CO₃) – Essential for new battery cathodes.
Cobalt Sulfate (CoSO₄) – High-demand material for EV batteries.
Nickel Sulfate (NiSO₄) – Critical for energy-dense NMC batteries.
Manganese Oxide (MnO₂) – Used in low-cost LMO batteries.
These products meet strict industry standards (e.g., ≥99.5% purity), ensuring seamless reintegration into battery supply chains.
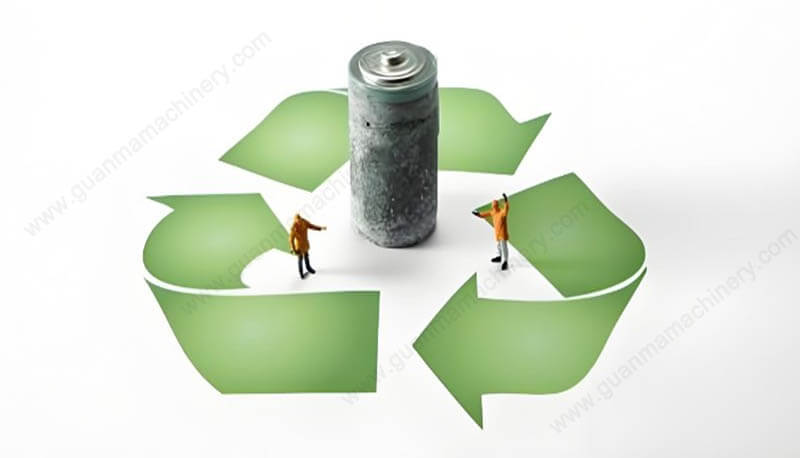
Why Choose Hydrometallurgy Process?
Higher Metal Recovery Rates: Up to 95–98% efficiency for critical metals vs. 50–60% in pyrometallurgy.
Lower Carbon Footprint: Minimal greenhouse gas emissions and energy consumption.
Cost Efficiency: Reduced operational costs through closed-loop reagent recycling.
Scalability: Adaptable for small or high-volume operations.
FAQs: Addressing Client Concerns
Q: How eco-friendly is hydrometallurgy?
A: The process uses closed-loop systems to neutralize waste acids and recycle water, complying with global environmental regulations.
Q: What’s the typical ROI for a hydrometallurgy plant?
A: ROI depends on metal prices and scale, but most plants break even within 3–5 years due to high-value output.
Q: Can you process mixed battery chemistries?
A: Yes! Advanced sorting and leaching systems accommodate diverse battery types.
Optimize Your Battery Recycling with Hydrometallurgy
For businesses aiming to capitalize on the booming EV and renewable energy markets, investing in a hydrometallurgy process for lithium-ion battery recycling is a strategic move. With high recovery rates, low environmental impact, and premium end-products, this method positions your company as a leader in sustainable resource recovery.