Is hydrometallurgy better than pyrometallurgy for battery recycling? The answer is yes. Understanding the core difference between pyro and hydrometallurgy, especially their pros and cons, is essential. Increasingly, hydrometallurgy is proving to be the superior solution for modern, sustainable, and high-yield battery recycling. Here’s why.
The Core Difference: Heat vs. Chemistry
At its heart, the difference between pyro and hydrometallurgy lies in their approach:
Pyrometallurgy
Relies on intense heat (often exceeding 1400°C) in furnaces to smelt battery black mass. This burns off organic components (plastics, electrolytes) and reduces metal oxides, typically producing a mixed alloy (like copper-nickel-cobalt) and slag. The process of pyrometallurgy is fast and can handle varied inputs, but it has significant drawbacks.
Hydrometallurgy
Uses carefully controlled aqueous chemical solutions (acids or bases) at relatively low temperatures (<100°C typically) to selectively dissolve valuable metals (lithium, cobalt, nickel, manganese) from the black mass. Impurities are removed through purification steps (like solvent extraction or precipitation), yielding high-purity individual metal salts or compounds ready for new battery production.
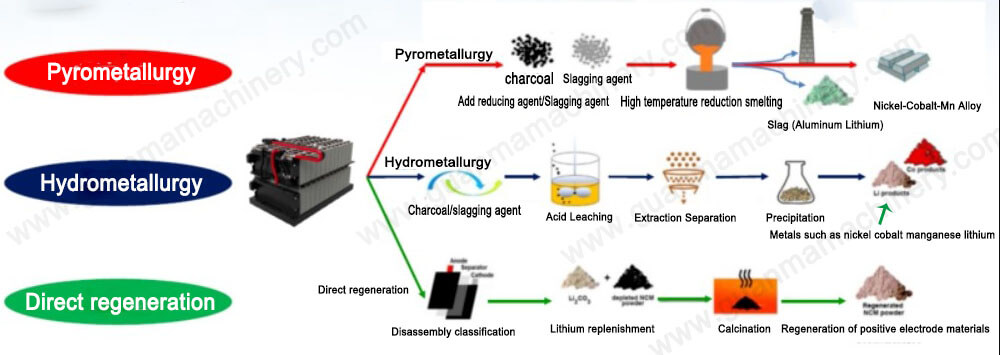
Why Hydrometallurgy is Gaining the Edge (Especially for Battery Recycling)?
Hydrometallurgy Advantages:
1. Superior Metal Recovery & Purity
One major advantage of hydrometallurgy over pyrometallurgy is its exceptional selectivity. It recovers lithium (Li), which is often lost in pyrometallurgical slag, and produces battery-grade cobalt sulphate, nickel sulphate, manganese carbonate, and lithium carbonate. These high-purity products command premium prices in the battery supply chain.
2. Lower Energy Consumption & Emissions
Operating at near-ambient temperatures drastically reduces energy needs compared to high-temperature furnaces. This translates to lower operating costs and a significantly smaller carbon footprint – a crucial factor for environmentally conscious businesses and regulations.
3. Enhanced Flexibility & Scalability
Hydrometallurgical plants can be more easily scaled to match your specific daily processing volume, whether you’re starting with 5 tons per day of Li-ion battery black mass or scaling up to 200 tons per day. Modular design facilitates expansion.
4. Handling Complex Feedstock
Modern battery chemistries (LFP, NMC, NCA, LCO) vary greatly. Hydrometallurgy’s chemical leach steps can be fine-tuned to efficiently extract valuable metals from diverse raw materials (spent EV batteries, consumer electronics batteries, manufacturing scrap), making it future-proof.

Addressing the Pros and Cons of Pyrometallurgy
Pyrometallurgy isn’t without merit. Pros of pyrometallurgy include faster bulk processing (especially for very high volumes initially), tolerance for some mixed or contaminated feed, and the destruction of organic components. However, its cons are significant:
Low Lithium Recovery
Lithium reports almost entirely to the slag, a low-value byproduct, representing a major loss of value.
Lower Purity Mixed Metal Output
Produces alloys requiring further complex refining (often using hydrometallurgy!) to separate individual metals for battery reuse.
High Energy Intensity & Emissions
Significant fossil fuel consumption and need for sophisticated, expensive gas cleaning.
Capital Intensity
Large, high-temperature furnaces represent major upfront investment.
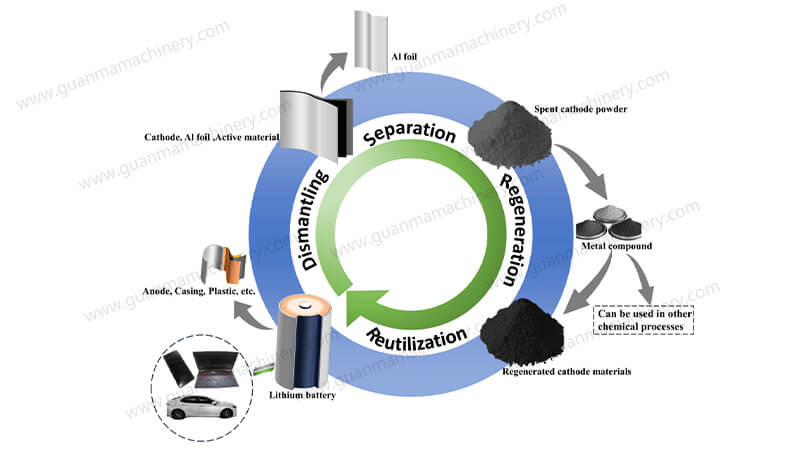
What is the Process of Hydrometallurgy in Battery Recycling?
Hydrometallurgy process
Feed Preparation: Crushed and sorted battery black mass (from mechanical pre-processing).
Leaching: Black mass is mixed with specific chemical solutions (e.g., sulphuric acid + reducing agent) to dissolve target metals (Li, Co, Ni, Mn) into solution.
Impurity Removal: Iron, aluminum, copper, and other impurities are precipitated out.
Solvent Extraction (SX): Specific extractants selectively separate cobalt, nickel, and manganese into different aqueous streams.
Precipitation/Crystallization: High-purity cobalt sulphate, nickel sulphate, manganese carbonate, and lithium carbonate are precipitated from their purified solutions. These are the final products – battery-grade raw materials ready for cathode manufacturing.
Effluent Treatment: Process waters are treated and recycled within the plant, minimizing waste.
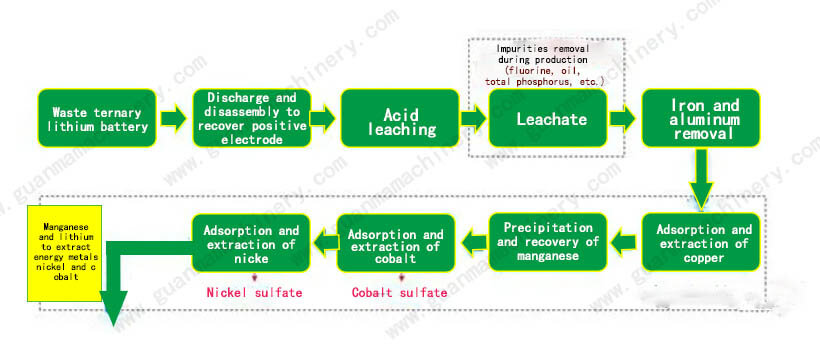
Optimizing Your Operation with Guanma Hydrometallurgy Solutions
Is hydrometallurgy better than pyrometallurgy for battery recycling? For recyclers prioritizing maximum value recovery (especially lithium), producing high-purity battery-grade products, minimizing environmental impact, and building a scalable, future-proof operation, the answer is a resounding yes.
Choosing Guanma Machinery means partnering with a leader in advanced hydrometallurgical technology. We design and build tailored systems that precisely match your raw material composition and desired daily processing volume, delivering the highest yields of valuable battery-grade cobalt sulphate, nickel sulphate, manganese carbonate, and lithium carbonate.