Struggling to find clear answers on silver refining machine cost? Investing in refining equipment is crucial for jewelers, recyclers, and mining operations dealing with silver scrap, doré bars, or concentrates. But prices vary wildly, making budgeting difficult.
Understanding the Price Range: It’s Not One-Size-Fits-All
Don’t expect a single price tag. Silver refining machine cost depends heavily on the type of refining technology, its capacity, and the level of purity you need. Here’s a realistic breakdown:
Chemical Refining Units (Acid-Based)
Cost Range: $5,000 – $25,000 USD
Best For: Smaller workshops, jewelers processing moderate amounts of silver scrap (e.g., bench sweeps, filings, low-karat jewelry).
Pros: Lower initial investment, simpler operation for basic purification.
Cons: Uses strong acids (nitric acid), requires strict safety protocols (fume hoods, PPE), chemical disposal costs, typically achieves 99.5% – 99.9% purity. Output is often silver chloride needing further conversion.
Key Cost Factors: Tank size/material (PP, PVDF), fume extraction system, included safety features, automation level for chemical dosing.
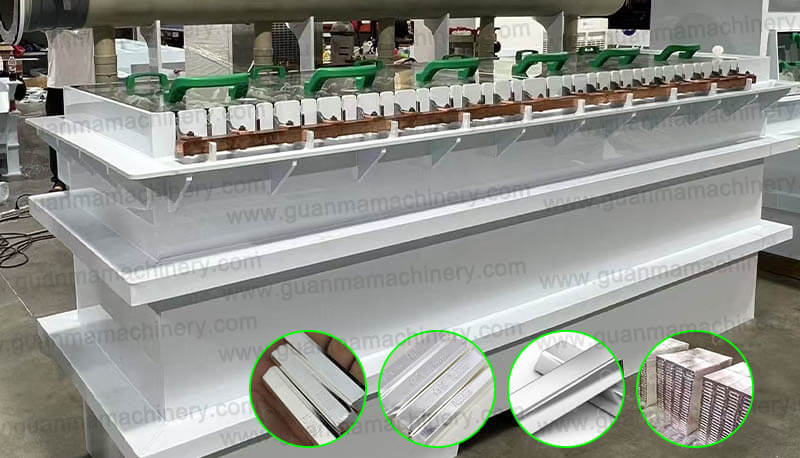
Small to Medium Electrolytic Refining Systems
Cost Range: $15,000 – $50,000 USD
Best For: Medium-scale operations (larger jewelers, dedicated recyclers, small mines) needing higher purity (99.95% – 99.99%+) and direct production of fine silver crystals or bars.
Pros: Higher purity output, more environmentally friendly than chemical-only methods (less chemical consumption), produces directly marketable silver. Often preferred for industrial silver refining equipment.
Cons: Higher upfront cost, requires stable power supply, electrolyte management needed.
Key Cost Factors: Number and size of cells, power supply capacity, material of construction (titanium, high-grade plastics), automation (rectifier control, electrolyte circulation), included casting equipment.
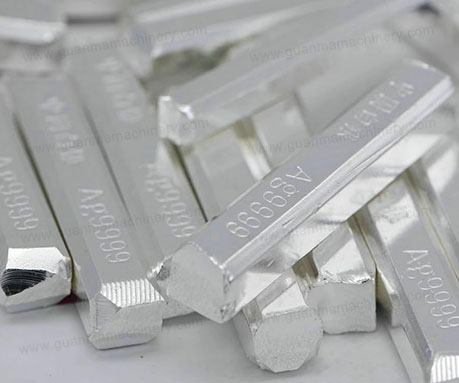
Large-Scale & Advanced Refining Plants
Cost Range: $50,000 – $150,000+ USD
Best For: High-volume refineries, large mining operations, electronic scrap processors requiring maximum purity (99.99%+), high throughput, and integration with other processes (e.g., gold refining).
Technology: Often combines methods – initial chemical leaching/dissolution followed by advanced electrolysis or precipitation. May include vacuum distillation units for ultra-high purity.
Pros: High automation, large capacity, superior purity, efficient recovery rates, lower operating cost per ounce at scale.
Cons: Very significant capital investment, requires skilled operators, substantial space, complex installation.
Key Cost Factors: Custom engineering, reactor vessel size/number, advanced control systems (PLC/SCADA), material handling systems (pumps, filters), precious metal recovery systems (e.g., for PGMs), pollution control systems (scrubbers).
Critical Factors Influencing Your Total Cost
Understanding these variables is key to comparing quotes accurately and finding affordable silver refining solutions that truly fit:
Capacity & Throughput
How many kilograms or tonnes of material do you need to process per day/week? A machine sized too small creates bottlenecks; too large wastes capital.
Target Purity
Standard sterling recovery (92.5%) costs less than achieving 99.99% fine silver for investment bars. Higher purity demands more sophisticated (and costly) technology.
Feed Material Complexity
Simple sterling silver scrap is easier and cheaper to refine than mixed electronic scrap containing base metals, solders, or other precious metals. Complex feeds may require pre-treatment stages, increasing system cost.
Automation Level
Manual systems cost less upfront but require more labor. Semi-automatic or fully automatic silver recovery machines command higher prices but boost efficiency, consistency, safety, and reduce long-term labor costs.
Material of Construction
Resistance to harsh chemicals (acids, chlorides) is vital. PP tanks are common, but PVDF or titanium components for critical parts (anodes, cathodes, heating elements) add cost and durability.
Safety & Environmental Compliance
Integrated fume scrubbers, spill containment, advanced filtration, and automated chemical handling increase safety and reduce environmental liability but add to the initial silver refining equipment price. Don’t underestimate these costs – they are essential.
Brand Reputation & Support
Established manufacturers with proven reliability and strong after-sales service (installation, training, spare parts, technical support) often command a premium but offer significant long-term value and reduced downtime risk.
Power Requirements
High-power electrolytic systems may need upgraded electrical infrastructure, adding hidden costs.
Installation & Commissioning
Factor in potential costs for shipping, foundation work, utility connections, and professional setup/calibration.
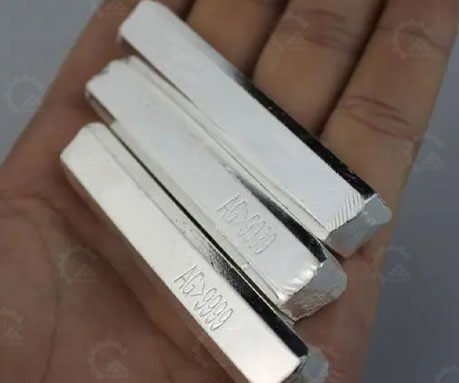
Finding the Right Balance: Cost vs. Value for Your Silver Refining Needs
The cost of silver refining machine is a significant investment, but focusing solely on the lowest price can be costly in the long run. Consider:
Return on Investment (ROI)
How quickly will the machine pay for itself through recovered silver value and increased processing efficiency? Higher purity often commands better market prices.
Operating Costs
Factor in consumables (chemicals, filters, power), labor, maintenance, and waste disposal. An efficient, automated system might have a higher upfront cost but lower operating expenses.
Scalability
Will your needs grow? Investing in a slightly larger or modular system now might be cheaper than replacing it entirely in two years.
Reliability & Uptime
Downtime means lost revenue. Quality machinery with good support minimizes this risk.
Get an Accurate Quote Tailored to YOU
To understand the real silver refining machine cost for your specific situation, provide potential suppliers with detailed information:
Type and volume of your silver-bearing materials (scrap, doré, concentrates).
Your required daily/weekly processing capacity.
Your target purity level (e.g., 99.5%, 99.9%, 99.99%).
Your available space and utilities (power, water).
Your desired level of automation.
Ready to Invest in Your Silver Future?
Understanding the variables behind silver refining machine cost empowers you to make a smart investment. Whether you need a compact unit for jewelry waste or a large-scale industrial silver refining solution, the right equipment boosts your recovery rates, purity, and profitability.
Request a Custom Quote Today! Tell us about your refining needs and discover the most efficient and cost-effective silver purification system designed for your success.