Establishing a black mass recycling plant setup is increasingly seen as a strategic and profitable venture within the circular economy. The explosive growth of electric vehicles (EVs) and consumer electronics has created a tidal wave of spent lithium-ion batteries. This surge presents a critical challenge – responsible disposal – and a massive opportunity: black mass recycling.
Understanding the Black Mass Opportunity
Black mass is the valuable, crushed material extracted from spent lithium-ion batteries, containing critical metals like lithium, cobalt, nickel, and manganese. Instead of mining virgin resources, black mass processing equipment allows for the recovery of these high-demand materials, feeding them back into the battery supply chain. Demand for recycled battery materials is skyrocketing, driven by regulations and OEM sustainability goals.
Key Costs in Black Mass Recycling Plant Setup
Setting up a plant requires significant investment. A thorough cost analysis is vital:
1. Facility & Infrastructure
Costs vary drastically by location, size, and local regulations (permitting, environmental compliance). Retrofitting existing industrial space can save capital expenditure (CapEx) versus new builds.

2. Lithium Battery Recycling Machine Core Processing Equipment (Major CapEx)
This is the heart of your lithium-ion battery recycling operation:
Discharge & Dismantling: Safe battery discharge systems and (often semi-automated) dismantling lines.
Crushing: Robust shredders and granulators to break down batteries into smaller fractions.
Separation Sophisticated systems (sieves, air classifiers, magnetic separators, eddy current separators) to isolate black mass powder from casings, copper, aluminum, and plastics.
Dust & Fume Control: Essential high-capacity extraction and filtration systems (HEPA, activated carbon) for safety and environmental compliance.
Hydrometallurgical/Pyrometallurgical Units (Optional On-Site): Further refining black mass into battery-grade salts or metals significantly increases CapEx but also potential revenue. Many plants sell black mass to dedicated refiners.
3. Ancillary Equipment
Material handling (conveyors, forklifts), storage (safe, fire-rated for batteries and black mass), laboratory (ICP-MS for analysis), safety systems (fire suppression, gas detection).
4. Operational Expenditure (OpEx)
Raw material (spent battery) sourcing logistics, energy consumption (high for shredding/pyro), labor (skilled technicians, chemists if refining), maintenance, consumables, waste disposal (non-recyclable fractions), compliance monitoring.
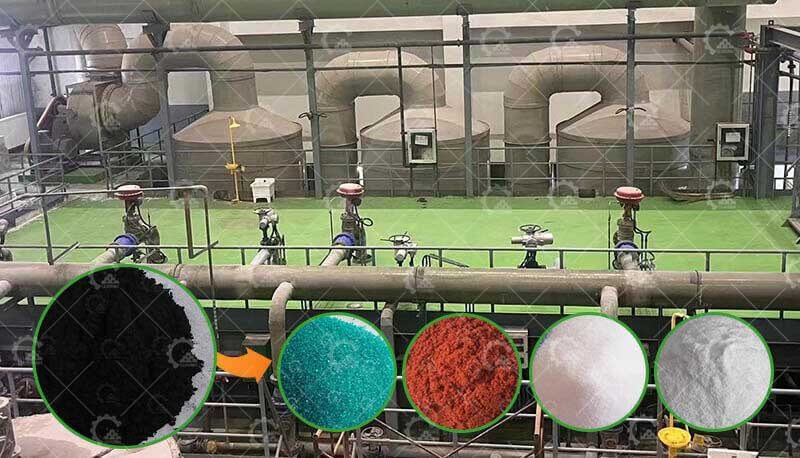
Essential Black Mass Processing Equipment
Investing in the right black mass processing equipment is non-negotiable for efficiency, safety, and product quality:
Pre-treatment: Battery discharge baths, thermal treatment units (for electrolyte removal/stabilization).
Primary Shredding: Heavy-duty, sealed shredders designed for battery hazards (sparks, fires, toxic gases).
Secondary Granulation: Further size reduction.
Mechanical Separation Line: The core of black mass extraction:
Vibrating Screens: Separate coarse and fine fractions.
Air Classifiers: Separate light materials (foils, plastics) from heavier fractions.
Magnetic Separators: Remove ferrous metals (steel).
Eddy Current Separators: Remove non-ferrous metals (copper, aluminum).
Filtration & Air Handling: Sophisticated systems to capture hazardous dust and fumes.
Automation & Control Systems: Ensure process stability, efficiency, and safety monitoring.
Profitability Analysis: Crunching the Numbers
The profitability of battery recycling hinges on several dynamic factors:
1. Feedstock Cost & Supply
Securing consistent, cost-effective volumes of spent batteries is crucial. Partnerships with collectors, OEMs, or waste handlers are key.
2. Black Mass Market Value
Prices fluctuate based on contained metal prices (Co, Ni, Li especially) and black mass purity/concentration. Regular market analysis is essential.
3. Processing Efficiency & Recovery Rates
Higher yields of valuable black mass and recovered metals directly boost revenue. Optimizing your battery recycling process flow is continuous.
4. Operational Scale
Larger plants benefit from economies of scale, spreading fixed costs (CapEx, management) over greater output.
5. Value Addition
Selling refined battery-grade materials (sulfates, carbonates) commands significantly higher prices than black mass, but requires major additional investment in hydromet or pyro refining.
6. Operational Costs
Minimizing energy use, labor costs, maintenance downtime, and waste disposal fees is vital for margins.
7. Regulatory Incentives/Subsidies
Government grants, tax breaks, or extended producer responsibility (EPR) schemes can significantly improve EV battery recycling business economics.
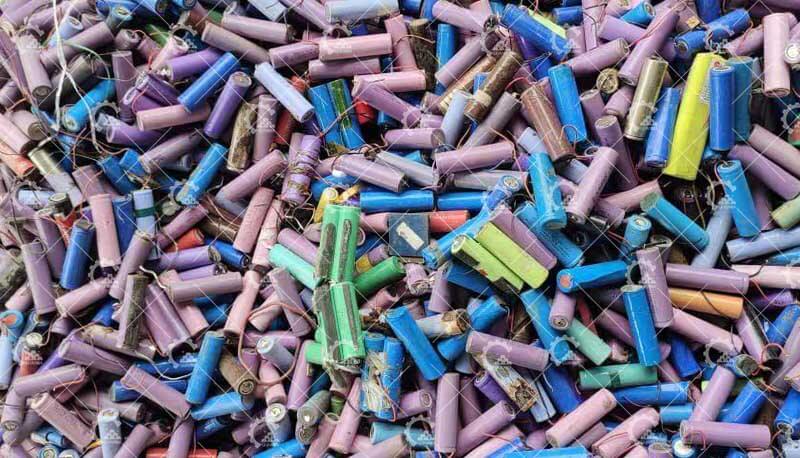
Is it Profitable?
While margins can be attractive, especially during periods of high metal prices, black mass recycling plant setup is a capital-intensive, technically complex, and operationally demanding business. Profitability is not guaranteed and requires:
Meticulous Planning: Thorough feasibility study and cost analysis.
Robust Technology: Investment in reliable, safe black mass processing equipment.
Secure Feedstock: Long-term supply agreements.
Off-take Agreements: Contracts for selling black mass or refined products.
Expertise: Skilled operational and technical teams.
Compliance Rigor: Meeting stringent environmental, health, and safety standards.
Establishing a black mass recycling plant setup represents a forward-looking investment in the sustainable battery economy. Success demands careful planning, securing reliable battery feedstock, investing in efficient and safe black mass processing equipment, optimizing the battery recycling process flow, and navigating complex regulations. For those prepared to meet these challenges, building an EV battery recycling business focused on black mass extraction offers a pathway to both environmental impact and compelling financial returns in the burgeoning green tech sector. Position your business at the forefront of this essential resource revolution.