With projections indicating millions of tons needing responsible management by 2025, establishing a lithium battery recycling plant is no longer just an eco-conscious move – it’s a strategic and potentially lucrative business imperative.
Why 2025 is the Pivotal Year for Lithium Battery Recycling
Critical Material Security
Recycling is vital for securing domestic supplies of cobalt, lithium, nickel – essential for the energy transition and national strategies.
ESG & Circular Economy Dominance
Investors and consumers heavily favor businesses demonstrably advancing sustainability and closed-loop supply chains.
Feedstock Explosion
The first major wave of EVs from the early 2020s is reaching end-of-life, significantly boosting available battery volumes.
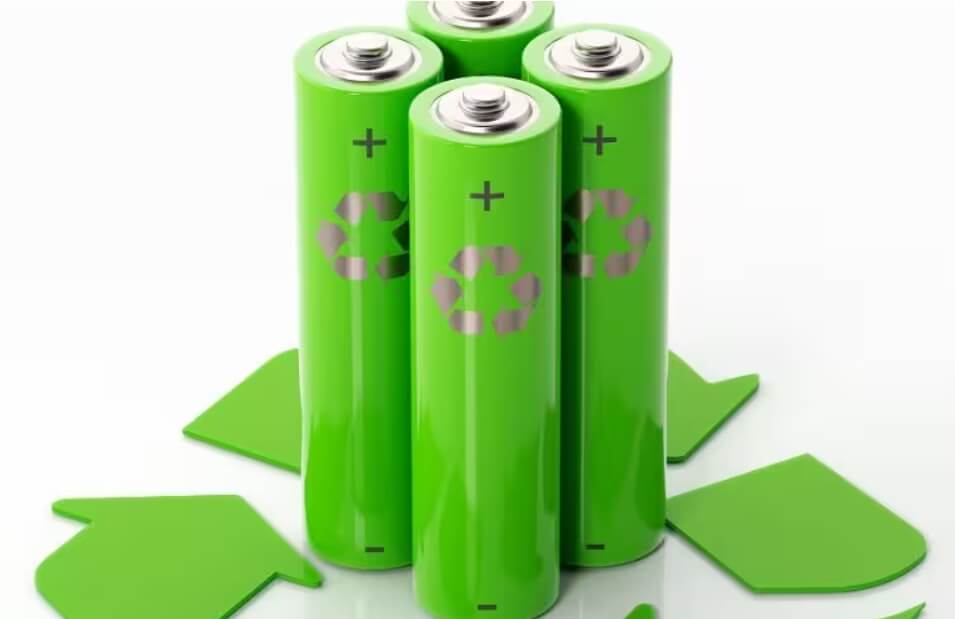
Your Step-by-Step Blueprint for 2025 Success
1. Deep Market & Regulatory Dive
Localize: Analyze specific feedstock sources (EV dismantlers, electronics recyclers, manufacturers) in your target region.
Master the Rules: Understand national/state environmental permits (hazardous waste handling, air/water emissions), fire safety codes (NFPA 855 is crucial), and evolving EV battery recycling regulations. Factor in future battery passport requirements.
Define Your Outputs: Target high-purity black mass (Li, Co, Ni) for cathode refiners? Recovered electrolytes? Plan based on offtake agreements.
2. Strategic Location & Scalable Design
Zoning & Logistics: Secure industrially zoned land with robust infrastructure (power, water, waste treatment), excellent transport links, and buffer zones. Consider proximity to feedstock and markets.
Future-Proof Layout: Design for modular expansion and evolving lithium battery recycling plant technology. Prioritize safety segregation zones (storage, discharging, processing).
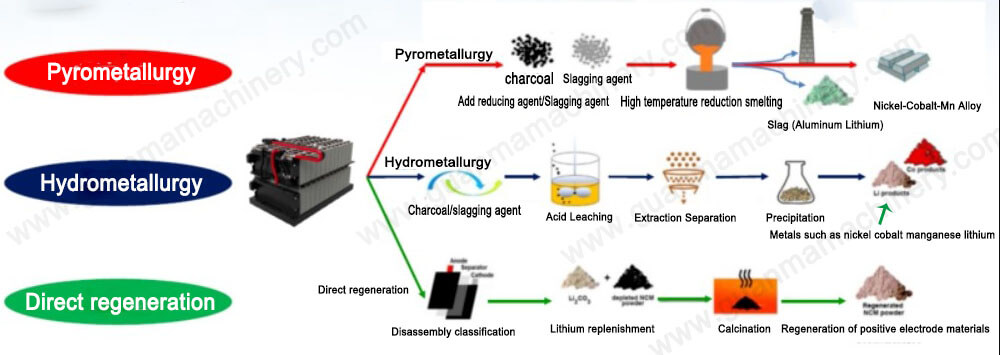
3. Selecting the Optimal Recycling Technology
Mechanical Pre-Processing (Essential First Step): Safe size reduction and component separation (shredding, crushing, sorting).
Hydrometallurgy (Dominant for High Purity): Chemical leaching and purification to extract high-value battery-grade metals. Offers superior recovery rates (>95%) crucial for profitability.
Pyrometallurgy (Established, High Energy): Smelting for bulk alloy recovery. Often combined with hydrometallurgy for refining.
Direct Recycling (Emerging): Cathode material recovery with minimal processing. Monitor sustainable battery recycling trends for 2025 viability.
4. Partnering for Core Technology: Guanma Machinery’s Turnkey Edge
Integrated Expertise: We provide the complete mechanical backbone: advanced shredders, hammer mills, specialized crushing systems, and highly efficient sorting lines (eddy current, air, vibratory) designed specifically for complex LIB packs.
Safety Engineered: Our systems incorporate inert gas suppression, explosion-proofing, and comprehensive dust/fume control meeting strictest 2025 safety standards.
Maximized Recovery, Minimized Cost: Precision engineering ensures optimal liberation of valuable materials, directly boosting your bottom line. Our modular hydrometallurgical recycling solutions integrate seamlessly.
Scalable & Compliant: Plants designed for growth and adherence to evolving lithium-ion battery recycling standards.
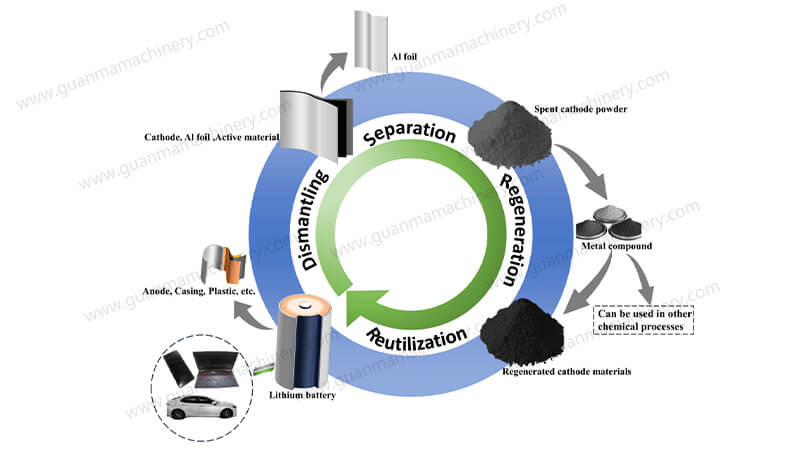
5. Navigating the 2025 Cost Landscape (Key Investment Areas)
Cost Category | Key Components | Estimated Range (USD Millions) | Notes
Processing Equipment (Core) | Shredding, Crushing, Sorting Lines (Guanma), Hydrometallurgical/Pyro Modules | $2M – $15M+ | Largest variable. Scale, tech choice (hydro vs pyro), automation level
Plant Construction & Fit-Out | Building, Utilities (High Power!), Ventilation, Safety Systems, Lab | $1M – $5M+ | Renovation vs. greenfield, safety compliance costs significant
Permits & Licensing | Environmental, Hazardous Waste, Air/Water, Fire (NFPA 855), Operational | $200K – $1M+ | Region-specific complexity, legal fees, can cause major delays
Working Capital & Feedstock | Initial Battery Inventory, Operational Costs (3-6 months) | $500K – $2M+ | Crucial buffer for market fluctuations & ramp-up
Staffing & Training | Engineers, Chemists, Skilled Operators, Safety Officers | Ongoing | Specialized skills essential; budget for rigorous safety training
Total Estimated Initial Investment: $4 Million – $25 Million+ (Highly dependent on scale, technology depth, and location).
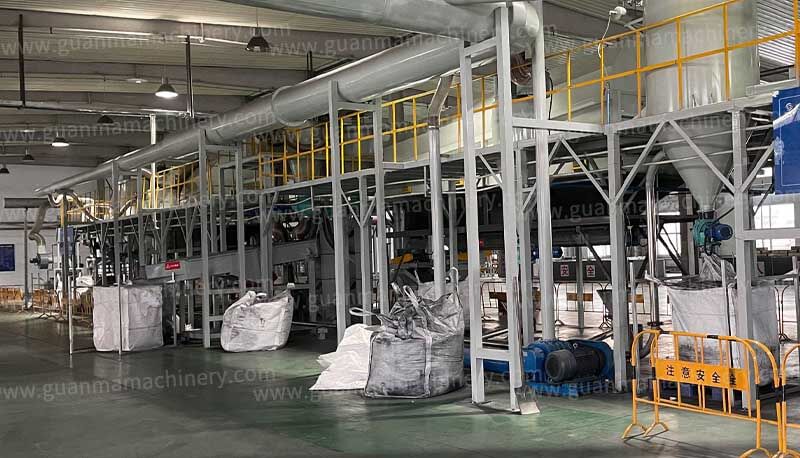
Why Partner with Guanma Machinery for Your 2025 Plant?
End-to-End Solutions: From initial plant layout consulting to supplying the core mechanical processing line and integrating with hydro/pyro partners.
Proven Technology, Optimized for 2025: Our equipment delivers industry-leading safety, recovery rates, and operational efficiency specifically for modern battery chemistries.
Cost Transparency & ROI Focus: Realistic budgeting and designs prioritizing your long-term profitability.
Global Compliance Support: Experience navigating complex international regulations.
Commitment to Innovation: Partners at the forefront of closed-loop battery recycling advancements.
Seize the 2025 Lithium Recycling Opportunity
The convergence of regulatory pressure, booming feedstock, and critical material demand makes 2025 the definitive year to enter the lithium battery recycling market. While the investment is significant, the long-term economic and environmental returns are compelling. Success hinges on meticulous planning, deep regulatory understanding, selecting the right technology, and partnering with reliable experts.
Ready to build your future-proof, profitable lithium battery recycling plant?
Contact Guanma Machinery TODAY for a detailed 2025 feasibility study and customized equipment proposal. Let our engineering expertise turn your vision into a leading, sustainable, and compliant recycling operation. Don’t just recycle batteries – reclaim value and lead the circular economy.